Understanding the performance gap: how BREL and BRWL reports support compliance
The Building Regulations require all new homes in England and Wales to meet specific energy efficiency standards, both at the design stage and after construction.
U-value Calculator
Start your U-value calculation
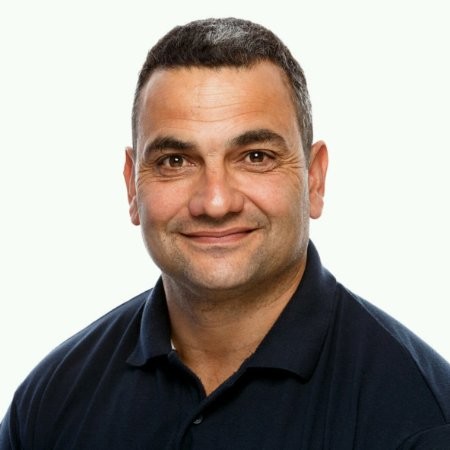
The Building Regulations require all new homes in England and Wales to meet specific energy efficiency standards, both at the design stage and after construction. A key challenge of this process is bridging the ‘performance gap’ – the difference between a building’s designed energy efficiency and its actual performance once built. To address this challenge and verify performance, BREL and BRWL reports have been introduced. In this guide to BREL and BRWL reports, we will explain what they are, why they matter and how manufacturers like Celotex support specifiers, architects and builders in meeting evolving efficiency requirements.
What are BREL and BRWL?
BREL and BRWL refer to the Building Regulations (England) Part L and Building Regulations (Wales) Part L, respectively. Part L covers the conservation of fuel and power, focusing on energy efficiency and reducing carbon emissions. The associated Approved Document sets out the requirements for buildings to ensure they are energy efficient.
- England: Approved Document L, Conservation of fuel and power: 2021 edition incorporating 2023 amendments
- Wales: Approved Document L, Conservation of fuel and power: 2022 edition incorporating 2024 amendments
The Approved Documents for both England and Wales are separated into two volumes. Volume 1 for dwellings and Volume 2 for buildings other than dwellings.
Part L encourages a ‘fabric-first’ strategy, with an emphasis on enhancing thermal efficiency, such as including high levels of thermal insulation, as well as air tightness. It also considers other factors such as thermal bridging, thermal bypass, renewable energy systems and efficient building services like heating, cooling, lighting and ventilation systems.
What are BREL and BRWL compliance reports?
For new-build dwellings, project teams must submit a series of documents to demonstrate compliance with the requirements of Part L and confirm:
- Which energy efficiency measures are proposed at the design stage
- That the energy efficiency measures are installed as designed
- Details of any changes made between the design and construction stages
These mandatory documents – known as BREL reports or BRWL reports – must be submitted to Building Control at key stages in the project. David Milner, technical team lead at Celotex, explains: “These reports are critical for demonstrating compliance during both the planning and construction stages. Failure to comply with these reporting requirements could result in significant delays or refusal to issue a Completion Certificate, and potentially expensive remedial works.”
For buildings other than dwellings, a similar document called the BRUKL (Building Regulations UK Part L) report is required.
Why are BREL and BRWL compliance reports required?
Introduced as part of the 2021 updates to Approved Document L, BREL and BRWL reports were designed to increase accountability, improve construction quality and ensure regulatory compliance. One of the main issues that BREL and BRWL reports address is the performance gap. David explains: “The performance gap is the difference between a building’s design and its actual energy performance once construction is complete. It can be caused by various factors, such as product substitutions, insufficient detailing or poor installation methods.” To help close this gap, BREL and BRWL reports, along with all necessary documentation, including photographic evidence (which provides essential proof of good installation), must be submitted to Building Control.
When are BREL and BRWL reports submitted?
BREL and BRWL reports are required for all new-build projects in England and Wales. They are not necessary for refurbishments, although Part L does outline energy efficiency requirements that must be followed for refurbishment projects.
For new-build projects, BREL and BRWL reports are submitted at two key stages:
- Design stage report – Submitted during the application phase and must be approved before construction begins. It demonstrates how the building is expected to comply with Part L, including proposed building fabric specifications, building services and predicted energy performance.
- As-built report – Submitted after construction is completed and required before final sign-off. It includes evidence that the planned energy efficiency measures were installed as designed. It also provides details on any deviations from the original design, along with updated energy performance calculations for the finished build.
What evidence should be included in BREL and BRWL reports?
A comprehensive collection of evidence makes it easier for Building Control to verify compliance and reduces the risk of delays at sign-off. Appendix B of Approved Document L sets out a list of reporting evidence required.
During the design stage, the software used for generating SAP assessments (Standard Assessment Procedure) can produce reports for BREL and BRWL.
David says: “These reports will show the target primary energy rate, emission rate and fabric energy efficiency rates that the building must achieve and the expected performance of the building.” He notes that the modelling software considers all parts of the building: “This includes the specified insulation details, such as heat loss from thermal bridging.” The report should also include a supporting list of specifications.
The as-built report needs to show that the building has been constructed as designed and clearly identify any changes from the design-stage report. Evidence and supporting documentation should be comprehensive to avoid delays.
David emphasises the importance of photographic evidence in the as-built report. “Photographs should clearly show the construction layers, including insulation thickness, that will not be visible once the building is complete. That’s why it’s essential to collect photographic evidence throughout the construction phase.”
Appendix B provides extensive guidance on producing photographic evidence. It states that photographs do not need to be taken by a qualified assessor, but it is essential that the images be unique for each property. So the same pictures cannot be used for multiple buildings, even if the structures were designed and constructed using the same materials at the same time.
Other evidence should also be provided, such as:
- Commissioning reports
- Installation certificates
- Product data sheets, including thermal properties
- U-value calculations for external walls, glazing and party walls ● Air permeability test reports
- Thermal bridging assessments
- Evidence of lighting performance
- Evidence of renewable energy installations and performance, such as solar PV, solar hot water and community heating systems.
- Confirmation of air tightness measurements
BREL and BRWL and the importance of product assurance
The aim of BREL and BRWL reports is to verify a building’s designed and as-built performance, ensuring that what’s specified in the SAP assessment is actually delivered on-site. However, all of this relies on the building products performing as expected.
With insulation being one a key contributor to building fabric performance, correct specification and installation are essential for achieving the required U-values.
Thermal bypass – heat escaping through gaps in or around the insulation – is a common reason for a building’s poor performance. To avoid this, insulation should be correctly installed according to the manufacturer’s instructions. This is why good product support plays a crucial role in product assurance and overall building performance.
Insulation manufacturers are responsible for ensuring their products perform consistently and are provided with clear installation guidance. David explains: “U-value calculations assume that insulation is installed without gaps, compression or voids. If that standard isn’t met, the assumed thermal performance in the SAP model may not be achieved.” This could lead to a project struggling to achieve compliance in its as-built report.
To help minimise this risk, specifiers should choose products from manufacturers who provide verified product performance data and comprehensive in-depth technical support, clear installation instructions, on-site toolbox talks and other resources to reinforce best practice. “This kind of support can directly impact compliance outcomes,” explains David. “It ensures installation quality and gives Building Control clear evidence that thermal performance has been prioritised throughout the design and build processes.”
What does the future of BREL and BRWL reports look like?
The current BREL and BRWL requirements are based on the 2021/2022 editions of Approved Document L. With the Future Homes and Buildings Standard (FHBS) expected to come into force later this year, new homes in England will soon be required to meet even more ambitious energy efficiency targets. While Wales (as well as Scotland and Northern Ireland) will not be affected by the FHS, more rigorous requirements are expected in years to come.
While the specifics of the new technical guidance have not been finalised, it's anticipated that the Future Homes Standard will lead to changes in the BREL reporting process. For example, SAP will eventually be replaced with HEM – the Home Energy Model, a cloud-based tool that is expected to require earlier design input and feature half-hourly energy simulations. To smooth the transition, SAP 10.3 is currently being developed as an interim solution while HEM, which is expected to replace SAP as the compliance methodology for new homes under the Future Homes Standard, is finalised. Whatever the upcoming changes entail, working with product suppliers that offer comprehensive technical support, including product testing and calculations, will be valuable in navigating evolving requirements and achieving compliance.
Celotex: helping you meet BREL and BRWL requirements
Producing compliant BREL and BRWL reports relies on having products with consistent, certified thermal performance, accurate technical information and high-quality installation. Celotex offers a range of resources to support specification and Part L compliance. These include:
- Comprehensive product datasheets
- A U-value calculator
- A dedicated technical support team that can assist with design, detailing and SAP-related queries.
To find out more about the Celotex range of thermal insulation products, including free consultations or sample requests, please get in touch.