What is cavity wall insulation?
Masonry cavity wall construction dates to the early 1900s. Since then it has become the predominant method for constructing the external walls of low-rise buildings, and housing in particular.
U-value Calculator
Start your U-value calculation
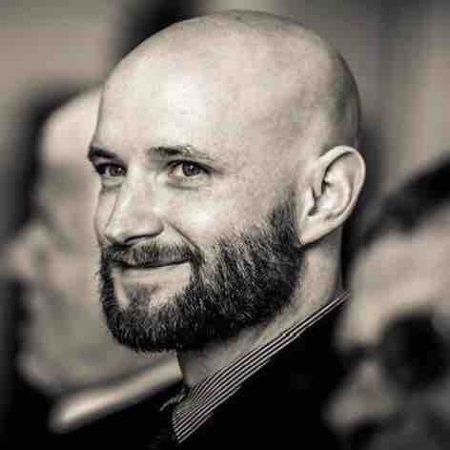
Masonry cavity wall construction dates to the early 1900s. Since then it has become the predominant method for constructing the external walls of low-rise buildings, and housing in particular. Different cavity wall insulation solutions were developed as energy efficiency requirements in national building regulations began to require lower U-values.
The pursuit of new insulation solutions has continued, allowing cavity walls to remain widely used in traditionally built housing even as energy efficiency targets have continued to tighten. With external walls accounting for around 35% of building fabric heat losses, how to build and insulate cavity walls must be a deliberate decision – one which this guide aims to assist with.
What is a masonry cavity wall?
For the purposes of this guide, “masonry cavity wall” means a wall with an outer skin of brick or blockwork, and an inner skin of masonry (almost always blockwork in new construction).
A structural timber wall with insulation fixed to the external face of the frame, then an outer brick skin, is sometimes described as a cavity wall, but is very much a framed construction in conventional terminology.
The outer masonry skin may be constructed from natural or artificial stone. This has implications for the design of the wall which go beyond the scope of this guide, such as the use of backing blocks or alternative systems. Natural stone, with its inherent variations in thickness, impacts on how the clear cavity is maintained, and it is recommended to seek specialist advice to achieve the best outcomes.
Why are cavity walls used in construction?
The traditional nine-inch solid brick wall suffered from several issues. Homes were already hard to heat, but the poor thermal performance of the walls also caused a risk of condensation on the inside of the wall.
In addition, rain ingress was a problem – especially in areas of very severe exposure, but also where brick and mortar had started to deteriorate.
As a result, the nine-inch ‘single brick’ wall became two ‘half brick’ leafs tied together but separated by an air cavity. For decades, the cavities in cavity walls were left clear (empty). There were no energy efficiency regulations requiring a certain level of thermal performance, and the insulation materials we now routinely use did not exist.
The air cavity helped manage external moisture ingress by providing a break in the moisture path and allowing any water that entered to drain or evaporate. Its thermal resistance also contributed to some improvement in overall thermal performance. In turn, this raised the wall’s internal surface temperature and helped reduce the risk of surface condensation.
How do I know if I have cavity wall insulation already?
During the 1960s and 70s, thermal performance requirements were introduced into building regulations for the first time, and then subsequently tightened. Over time the ‘brick and brick’ cavity wall became the ‘brick and block’ cavity wall, and insulation materials started to be incorporated into house designs to further boost thermal performance.
Introducing a 50mm cavity between two skins of four-inch (approx. 100mm) masonry increased the overall wall thickness to around 250mm. In the early 2000s it was not uncommon to specify 285mm cavity walls to meet thermal performance targets, and then 300mm in the 2010s.
Depending on the level of performance desired from a wall, currently it may be necessary to look at a cavity width of 150-200mm to accommodate sufficient insulation. That carries its own challenges.
“The main driver of cavity wall design and insulation product development continues to be regulatory,” says David Milner, Technical Team Lead at Celotex. “With each revision to the building regulations, the combination of brick, insulation and block type has altered to meet the new targets, all while seeking to maintain familiar construction methods for contractors and developers.”
How does cavity wall construction support building regulations compliance?
This section of the guide summarises the principles of safe building design and construction for areas of regulation that apply to cavity wall construction. For advice on compliance with specific requirements in a specific country of the UK, it is always recommended to consult with building control bodies and inspecting authorities.
England and Wales traditionally shared regulations, until devolved powers allowed Welsh Ministers to set their own. Many regulations remain common, but Part B and Part L were among the first areas to be looked at separately. Scotland and Northern Ireland, meanwhile, maintain their own building regulations.
- Structure
Approved Document A, England and Wales; Section 1, Scotland; Technical Booklet D, NI
Essentially, the inner skin of a masonry cavity wall bears the structural loads of the roof and intermediate floors down to the foundations. The outer skin does not carry as much load but aids the stability of the wall as a whole and must be adequately tied to the inner skin.
The technical guidance published to support regulatory requirements covers selecting wall ties. They are one of the few items accepted as being able to bridge a cavity – and therefore the insulation layer – along with cavity trays, cavity barriers, fire stops and cavity closers.
Cavity wall insulation solutions do not serve a structural function, so regulations relating to structure have little to no impact on product choices. The technical guidance does influence the wall design into which the insulation must be fitted, such as the minimum thicknesses of individual masonry skins.
- Fire
Approved Document B, England and Wales; Section 2, Scotland; Technical Booklet E, NI
A key part of fire safety regulations is dividing buildings into discrete compartments to restrict the spread of fire. Compartments are separated from one another by walls and floors made of a fire-resisting construction.
Cavity barriers are used within concealed spaces, like the cavity of a cavity wall, to hinder the unseen spread of fire or smoke from one compartment to another.
“The technical guidance supporting fire safety requirements sets out specific provisions for cavity barriers,” explains David Milner. “For example, cavity barriers are placed within cavity walls at the intersection of compartment walls and floors. These are manufactured from non-combustible glass mineral wool or stone mineral wool insulation.”
Cavity barriers are also required around openings, and at the top of cavities. For a cavity wall featuring two skins of brick or concrete, each a minimum thickness of 75mm, these cavity barriers do not need to achieve a specific level of fire resistance performance. Such products may be referred to as ‘cavity closers’ rather than ‘cavity barriers’. In addition, materials within the cavity, including thermal insulation, may include combustible materials where permitted under national regulations. The allowable use of combustible materials will depend on factors such as building height, purpose group, and applicable fire safety requirements.
- Resistance to moisture
Approved Document C, England and Wales; Section 3, Scotland; Technical Booklet C, NI
Suitable cavity wall constructions and insulation solutions for specific sites are determined by the exposure rating of the building’s location, adjusted for local conditions, and factoring in the proposed insulation type and the outer masonry skin.
Cavity wall insulation products should possess current certification from an appropriate body (most commonly the British Board of Agrément (BBA) in the UK) or a European Technical Approval and be installed in accordance with the certificate/approval. The certification describes the wall construction tested for resistance to external moisture, and the guidance should be followed to ensure the construction performs as tested and certified.
Blown insulation materials designed to be installed after the wall has been constructed should be certified and installed accordingly. Where they are being installed in an existing building, the quality and condition of the outer skin should be assessed regarding the location of the building and its exposure.
- Combustion appliances
Approved Document J, England and Wales; Section 3, Scotland; Technical Booklet L, NI
Regulations require certain distances to be maintained between combustible materials and chimneys or flues, where the heat dissipated by appliances might be significant.
Where combustible cavity wall insulation is installed near chimneys or flues, compliance with separation requirements must be demonstrated, taking into account the thickness of non-combustible masonry and the conditions within the cavity. Building control bodies may assess each situation based on the specific design and certification details provided.
Conservation of fuel and power / Energy
Approved Document L, England and Wales; Section 6, Scotland; Technical Booklet F, NI
Energy efficiency regulations are designed to reduce the overall energy demand of buildings. An important part of that is low U-values for individual building elements, and cavity wall insulation has a key role to play in the performance of external walls.
For new build projects, regulations take a ‘whole building’ approach. Compliance is determined by the complete package of measures specified, including thermally efficient building fabric. There are no fixed U-value targets, although regulations offer example specifications that will comply if replicated exactly. For most projects, those specifications will not be replicated and required U-values are determined by the compliance calculations for the proposed design.
Linear thermal bridging is another part of the overall ‘package’. When cavity wall construction is proposed, the design of junctions where the floor meets the wall, and where the wall meets the roof, should aim to achieve continuity of insulation through the building envelope. The detailing of these areas, as well as around openings for doors and windows, determines the psi values that can be used as part of the compliance calculations.
For the refurbishment or extension of existing buildings, U-value targets are more definitive but not as low as for new build projects. There is much less focus on thermal bridging, but it should remain a consideration during design and construction in the interests of demonstrating good practice and achieving design intent.
Energy efficiency is the biggest driver of insulation specification, so the next section looks at types of insulation solutions available.
What types of cavity wall insulation are available?
The introduction of thermal insulation into masonry cavity walls has led to consistent evolution of the way walls are designed and built, largely driven by the evolution of regulatory targets. Insulation manufacturers have sought to develop solutions that can achieve low U-values without compromising the other regulatory areas discussed above. The most common solutions are summarised here.
• Rigid foam insulation boards – partial fill
Almost exclusively, these solutions are manufactured from polyisocyanurate (PIR) or phenolic foam. The low-density material makes the boards comparatively lightweight and easy to handle, especially as they are sized to suit conventional wall tie spacing and therefore much smaller than boards offered for other applications.
A key characteristic of these products is their thermal performance, with most commonly available products having a lower thermal conductivity than alternative insulation materials. In addition, partial fill boards feature an aluminium foil facing that improves the thermal performance of the air cavity they face into.
Most boards are supplied with a square edge profile. When they butt against one another, the board joint offers a path for moisture to track through the construction and reach the inside of the building. An essential feature of partial fill insulation solutions, therefore, is the clear cavity that must be maintained between the outer masonry skin and the rigid insulation to manage moisture.
Traditionally, the residual clear cavity is 50mm wide, but third-party certification can give further advice on minimum requirements.
- Full-Fill Glass mineral wool and stone mineral wool batt
These are long-established insulation solutions that fully fill the wall cavity. The two types of mineral wool do not offer as low a thermal conductivity as the rigid foam insulation boards described above.
They can, however, use the entire cavity width and so in some instances are able to achieve comparable thermal performances to partial fill Rigid foam solutions.
Of course, this should always be checked by obtaining project-specific U-value calculations, since the type of masonry and the proposed internal finish will impact on the result.
The slight flexibility inherent in mineral and stone wool batts assists with installation, especially if some excess mortar protrudes into the cavity and results in a surface that isn’t completely flat, or if the overall cavity width varies for any other reason.
Full fill batts are also sized to fit between conventional wall tie spacings and compress slightly at joints to limit gaps once butted up to one another. During manufacture, the material fibres are spun together and the composition of the finished products, combined with this knitting together, makes them resistant to water transmission across the cavity when correctly installed.
- Rigid foam insulation boards – full fill
In recent years, rigid insulation manufacturers have experimented with new innovations to offer even lower U-values without changing the overall thickness of cavity walls or substantially altering the way they are built. To do this, they have focused on reducing the clear cavity and increasing the amount of insulation accommodated within the wall.
Rigid foam insulation boards designed for full fill applications are distinctly different from the flexible full fill batts described above.
With the removal of the clear cavity that manages moisture in a partial fill solution means the design of the insulation product must change to provide the barrier instead. In most systems, this is done with a rebated, rather than square, board edge profile.
Using an interlocking joint is designed to achieve a tighter fit between boards and limit the passage of water that might otherwise track across the insulation layer. The interlocking vertical edge profile further assists in managing water movement by reducing the potential for moisture tracking along board joints. For a wall construction featuring a 100mm cavity, the various systems on the market range from boards of 90mm to 97mm thick.
“Despite the fundamental difference in approach, there can be similarities between partial fill and full fill insulation board products,” says David Milner. “For example, some full fill boards still make use of the thermal benefit of aluminium foil facing into the small air cavity that remains. Nevertheless, the two should not be confused. Mistaking a partial fill board as suitable for a full fill application could lead to performance issues, particularly in relation to moisture management.”
It was always straightforward to distinguish between partial fill insulation boards and full fill insulation batts. The two types of solution used completely different materials. Full fill rigid boards have blurred that distinction, which might risk some confusion when a full fill batt is non-combustible, and a full fill rigid board is combustible. This difference is addressed through appropriate design and compliance with the relevant regulatory requirements.
- Blown insulation
None of the solutions above are suitable for existing properties. It is infeasible and uneconomical to open up cavities in such a way as to accommodate the installation of insulation boards or batts. Blown insulation is the primary method of filling an empty cavity as part of a retrofit project, though the suitability of the wall construction and the building location must be carefully assessed.
That doesn’t preclude blown solutions from being used on new build projects, and it is a common way of providing cavity wall insulation on volume housing sites.
Blown insulation should be installed under an approved scheme. Small holes are drilled through the outer leaf masonry and the insulation pumped into the cavity through a nozzle. The material used can be mineral fibres or EPS beads. As they bind together in the cavity, they form a structure that resists water penetration when used in the correct exposure areas.
How much does cavity wall insulation cost?
The range of stockists offering cavity wall insulation products is varied, from well-known national merchants with large branch networks to online outlets. Costs vary depending on supplier, and on an individual contractor’s terms with their preferred stockist.
In addition, material prices across the construction industry are often in a state of flux. Since the Covid pandemic, prices have risen and continue to be volatile.
In general, insulation products with lower thermal conductivity tend to have higher material costs per unit area, reflecting differences in raw materials and manufacturing processes. Being at the more thermally efficient end of the insulation spectrum, PIR cavity wall solutions typically have higher material costs compared to some alternative insulation types, reflecting the costs of raw materials and the technology required to manufacture them.
Understandably, thicker products are more expensive than thinner ones.
Despite all this, thermal insulation contributes to reduced energy demand for buildings. David Milner says: “The better the standard of energy efficiency achieved overall, the lower the lifetime energy demand. Insulation is an investment, and a high standard of installation is an investment. Material and labour costs will only ever increase, so the best time in any building project to get the level of insulation ‘right’ is the very start.”
How long does cavity wall insulation last?
Specified and installed correctly, cavity wall insulation can be expected to last for the life of the building. It should also deliver its intended performance throughout that time. Product-specific statements regarding durability can be found in third-party certification, like BBA certificates.
The subtle distinctions between the different types of insulation discussed above demonstrates how important it is that design professionals and specifiers understand the cavity insulation products they are selecting and explain those selections clearly to other parties.
In addition, the supply chain must ensure rigour in the purchasing (and any attempted substitution) of insulation products. Allied to that, contractors and installers should have robust quality control measures in place on site to ensure a high standard of installation.
It is essential to seek a manufacturer’s advice, about any of the types of cavity wall insulation discussed above, at the right time – and the sooner the better. Asking questions once products have been installed leads to expensive remedial works or flawed installations, neither of which are a desirable outcome.
Product literature and third-party certification should be the first port of call, supported by conversations with technical support teams.
Why is my house cold even with cavity wall insulation?
Poorly fitting cavity wall insulation boards allow air to circulate around them. Warm air from inside the building mixes with cold air in the wall cavity. Studies suggest that where this kind of thermal bypass takes place, increased heat loss of up to 160% can be expected compared to the calculated U-value.
To improve the likelihood of achieving a quality installation, sequencing the wall construction correctly is the best place to start. As the wall is built up in sections, starting with the inner skin allows for mortar squeeze to be cleaned off, giving a clean flat surface against which the insulation can be installed. A cavity board is always recommended to catch any mortar droppings and keep the cavity clean.
Insulation batts have some flexibility to accommodate undulations in the blockwork, but rigid insulation boards are less adaptable. Trying to force them against an uneven surface either risks damage to the board which can affect its thermal and moisture management performance.
All good practice advice and installation guidance for cavity wall insulation products provided by manufacturers and certification bodies emphasises the need to keep the cavity clean, since debris in the cavity increases the risk of external moisture reaching the inside of the building.
How does a low emissivity facing benefit foil-faced cavity insulation boards?
As touched on earlier, a key feature of rigid insulation boards facing a clear cavity is the aluminium foil’s ability to enhance the air’s thermal resistance. This contributes to achieving a lower overall U-value for the wall. The aluminium foil is classed as a low emissivity surface, compared to the high emissivity of other materials in the wall build up.
As David Milner explains: “A material’s emissivity determines the amount of thermal radiation emitted from its surface and depends on both the material itself and the condition of the surface. A clean metal surface has a lower emissivity than a dirty metal surface, so an attempt should be made to keep the face of insulation boards relatively clean as the wall is built up, to gain the declared low emissivity performance.”
The low emissivity properties of aluminium facings are established through product testing, and a value declared. The value is used in a U-value calculation to work out the thermal resistance of the air cavity. The highest thermal resistance value is for a cavity of 20mm or greater. However, cavities of less than 20mm can still see a benefit from low emissivity surfaces.
How should cavity wall insulation be installed around wall ties?
The design of cavity wall ties has changed a lot over the last century, from their shape to the material from which they are manufactured.
Modern wall ties will not corrode, and feature drips that stop moisture tracking along the tie to the inner masonry leaf – even when the drip sits within an insulation layer. Standard guidance recommends they should be installed with a slight downward slope to the external masonry leaf to discourage the potential passage of water.
To ensure the stability of the wall, wall ties should be installed in sufficient numbers and in the correct patterns. This is particularly true around openings, and the insulation manufacturer’s guidance should be followed accordingly.
Ties need to be placed on mortar beds prior to the next course of masonry being laid – not pushed in after the masonry has been built up. That means the correct sequencing of bricks, blocks, insulation, and ties needs to be followed.
Insulation boards and batts are sized to fit between wall ties at prescribed spacings and fixing densities. Wall ties should not be inserted through insulation products, as this can compromise both the continuity of the insulation layer and the moisture management function of the cavity. Penetrating the insulation with wall ties introduces unnecessary thermal bridging and increases the risk of moisture tracking across the cavity and should therefore be avoided.
There are four types of wall tie, each suited to a designed building load and cavity width. A type-1 wall tie is more substantial than a type-4 tie designed for low rise domestic construction. Selecting wall ties of appropriate size and profile for the structural requirements can help ensure insulation boards fit correctly and reduce the potential for gaps in the insulation layer.
How should cavity trays be installed with cavity wall insulation?
Where the flow of external moisture down the cavity will be interrupted by an obstruction (such as a lintel) or abutment, a cavity tray is required to direct the moisture away from the inner skin. The cavity tray spans from the inner to outer masonry leaf, which requires careful detailing around cavity wall insulation products to minimise the risk of the insulation layer becoming discontinuous.
Particular care needs to be taken with stepped cavity trays at pitched roof abutments. If in doubt, seek further advice from the insulation manufacturer, the cavity tray manufacturer, and any warranty provider (such as NHBC or LABC Warranty Standards).
What cavity wall insulation solutions are available from Celotex?
As a manufacturer of rigid PIR foam insulation boards, Celotex have insulation boards suitable for both partial fill and full fill cavity walls. Celotex CW4000 is a partial fill insulation solution, and Celotex Thermaclass Cavity Wall 21 is designed for both full fill and partial-fill applications. The following table summarises key product features of both.
Characteristic | Celotex CW4000 | Celotex Thermaclass Cavity Wall 21 |
Application | Partial fill cavity wall | Full fill cavity wall |
Thermal conductivity (W/mK) | 0.022 | 0.021 |
Board dimension | 1200 x 450mm | 1190 x 450mm |
Board edge profile | Square | Tongue and groove |
Low emissivity facing | Yes | Yes |
BBA certificate | 24/7312 | 24/7312 |
Thickness range | 40mm to 100mm | 90mm, 115mm and 140mm |
Height restrictions | Should not be used in the external walls of buildings over 11 metres in height. Building regulations require only non-combustible insulation or insulation of limited combustibility to be used in buildings of that height. |
To support the specification of Celotex cavity wall insulation products, designers and specifiers can obtain indicative U-value calculations from the Celotex free online U-value calculator. The Celotex online calculator has always been one of our most-valued tools. Its functionality has been improved, and it now offers condensation risk analysis alongside combined method heat loss calculations.
Users can calculate U-value calculations and, for construction types recommended by BS 5250:2021, condensation risk at their convenience. Technical specifications and installation resources for Celotex products are also available online, providing support for developing project-specific specifications, subject to regulatory and design validation.
For construction types not covered by the calculator, or for any advice relating to using Celotex products in a construction project, contact the technical support centre for further advice.
1https://blog.siga.swiss/gb-en/beware-thermal-bypass-its-air-behaving-badly & https://www.pmcarchitects.com/sustainability-information-blog-content/thermal-bypass-what-is-it