What’s the role of thermal insulation in preventing condensation in buildings?
Effective condensation control in buildings can be summed up as a three-pronged strategy: insulate correctly, provide adequate ventilation and manage the movement of moisture.
U-value Calculator
Start your U-value calculation
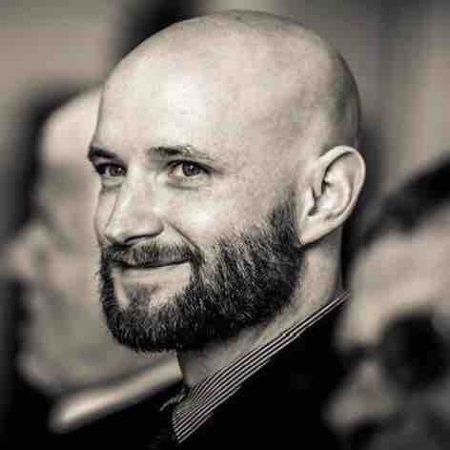
Effective condensation control in buildings can be summed up as a three-pronged strategy: insulate correctly, provide adequate ventilation and manage the movement of moisture. Specifying thermal insulation for condensation control is therefore just one – but very crucial – part of the holistic approach required.
The complexity of moisture management in buildings can mean that implementing these three elements is far from simple. In particular, designers and specifiers have no control over how the eventual occupants will use a building. That means building fabric specification and detailing decisions, together with appropriate ventilation solutions, are crucial.
How can architects and specifiers design out condensation risk in new-builds?
In new-build construction, modern techniques often use airtight, vapour-closed fabric specifications to prevent moisture from entering the building.
Rigid PIR insulation boards (and other similar thermal insulation products) can be well-suited to this approach, coupled with membranes such as vapour control layers (VCLs) and breather membranes. Once correctly sealed at seams and junctions, this forms the construction’s airtightness barrier to help control the movement of air and vapour.
Some new-build projects adopt a vapour-open approach. In most cases, however, vapour-open construction is encountered when dealing with traditional building fabric as part of retrofit projects. This requires the selection of different materials and the use of different methods of condensation risk analysis. Therefore, a closed cell material with a high vapour resistance facer like PIR is less likely to be used.
Addressing this important distinction goes some way to illustrating the mindset required when considering condensation risk in buildings. Preventing condensation risk isn’t one single solution. Nor is it something you can easily improvise in the later stages of a building project.
While you cannot tell the future occupants of a building how to live in or use it, you can design and specify with certain behaviours in mind. It’s an often-quoted statistic that we spend around 90% of our time indoors: the UK government states the figure is between 80% and 90% , while the EU puts the figure at 85-90%2 .
As David Milner, Technical Team Lead at Celotex, says:
“Since the Covid-19 pandemic, more people are working from home, either full-time or part-time. This is in addition to everyday activities like cooking, cleaning, bathing, and drying laundry, all of which generate moisture indoors. Without adequate ventilation, this can increase indoor humidity levels, raising the risk of condensation within the building fabric.
What causes condensation in buildings, and why is it a problem?
When we talk about condensation risk, we are really talking about two different types of condensation, surface condensation and interstitial condensation.
What is surface condensation?
Surface condensation refers to moisture that forms on the surface of a building element when warm, humid air comes into contact with a cooler surface. It may occur as a light dampness or, if the accumulation of moisture is large enough, it could form into droplets that run down the surface.
This process occurs when the surface cools the surrounding air below its dew point temperature, the point at which air can no longer hold all its water vapour, causing condensation to form on the surface. The dew point varies depending on the air’s temperature and relative humidity. Window panes are the most obvious example of surface condensation occurring, because window glass is usually significantly cooler than other surfaces. If a wall or ceiling is cool enough (or the air humid enough) for condensation to occur on its surface. This moisture can damage finishes, reduce thermal performance, increase maintenance needs, promote mould growth, and negatively impact occupant health.
What is interstitial condensation?
The same principles apply here to moisture-laden air coming into contact with a cooler surface. The difference is that interstitial condensation refers to the process occurring within the layers of the building fabric, rather than on exposed surfaces.
The obvious problem is that the condensation is unseen. If it is frequent enough and severe enough, then over time it can wet materials within the building’s structure. Thermal insulation materials can lose performance if they become wet; timber elements can begin to decay over a period of years.
“For interstitial condensation to occur there must be some failure in the vapour-closed nature of the construction,” explains David Milner. “There may be a penetration of the AVCL, allowing air and moisture to pass into the construction. That air then needs to meet a cooler surface to the external side of the insulation layer. Poor installation of insulation, which leaves gaps or voids, can also allow warm air to circulate to cold surfaces and increase the condensation risk.”
How do U-values and thermal performance relate to condensation risk?
Among the measures that can be employed to control condensation are raising temperatures: either of the air, or of building element surfaces.
Raising the air temperature increases its capacity to hold moisture, reducing the relative humidity and lowering the likelihood of condensation. However, relying on additional heating to achieve this may not be practical or affordable for many occupants.
A well-insulated building slows the transfer of heat through the building fabric. But we must also consider the movement of the heated air. If there are pathways in the fabric that allow warm air to escape, a significant proportion of heating energy can be lost through air leakage (exfiltration) and the entry of cold air (infiltration).
Airtightness is therefore also critical, alongside an appropriate insulation specification.
Coming back to the holistic approach, better airtightness should be paired with controlled and effective ventilation to ensure a supply of fresh air. This has the added benefit of helping to remove moisture vapour from the air, also contributing to the control of condensation.
David Milner adds: “Better-insulated building fabric with lower U-values slows the rate of heat loss and keeps surface temperatures warmer. When surfaces are warmer, humid air is less likely to cool below its dew point on contact, making surface condensation less likely.”
What are the best insulation solutions for condensation control?
Focusing on improving the insulation of the building fabric often leads to discussions about achieving lower U-values. While national building regulations such as Approved Document C (England and Wales) set a recommended maximum U-value of 0.35 W/m²K to help prevent surface condensation under typical conditions, energy efficiency standards, such as those in Approved Document L or voluntary schemes like Passivhaus, generally require much lower U-values. This means that designing and specifying insulation goes beyond just meeting minimum standards and plays a crucial role in reducing condensation risk.
Thermal bridges are areas in otherwise well-insulated building fabric where the continuity of insulation (and possibly of vapour control measures too) is interrupted. Learn more about this topic in our blog post about reducing thermal bridging.
“Discontinuity of insulation in the building envelope can create pathways for heat loss, which lower local surface temperatures and increase the risk of condensation,” notes David Milner. “And where insulation is not continuous, these cooler surfaces can become prime locations for both surface condensation and, in some cases, interstitial condensation if the air and vapour control layer is also compromised.
Getting thermal bridging right is just as important to condensation control as it is to complying with energy efficiency requirements. Little wonder, then, that BS 5250:2021 Moisture management in buildings - Code of practice provides detailed guidance on the importance of junction detailing and its role in moisture management.
How can Celotex help with thermal bridging solutions?
Celotex’s range of PIR insulation boards – including GA4000 and TB4000 – can be specified for floors, walls, and roofs to help achieve low U-values. When detailed correctly (including fixing details, service voids and vapour control measures as necessary), the boards can help to provide the continuous layers of insulation that limit the transfer of heat, reduce air leakage, and help maintain warmer internal surface temperatures.
The Celotex team of technical advisors is on hand to help specify the best solutions to meet insulation requirements. Additionally, the new Celotex online U-value calculator is available and designed to be user-friendly while offering advanced functionality, instant results, and visual outputs, which are also included in the downloadable calculation reports.
Regulatory compliance documentation, including performance certificates, is available through the Celotex Technical Resource Centre. Supported by this documented performance data, the technical services team offers verified calculations, construction details, and regulatory guidance to help develop accurate specifications for both standard and bespoke constructions.
2 https://ec.europa.eu/commission/presscorner/detail/en/ip_03_1278