The role of thermal bridging in energy efficient buildings
Thermal bridging heat losses have been part of energy efficiency regulations and compliance calculations in Approved Document L since 2006. With every regulatory update since, in all parts of the UK, thermal bridging’s role has become increasingly important.
U-value Calculator
Start your U-value calculation
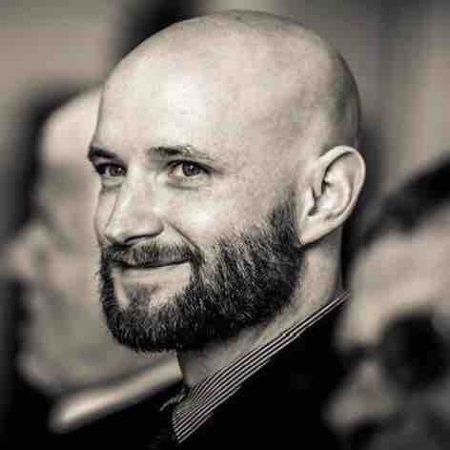
How can you reduce thermal bridging heat loss?
Thermal bridging heat losses have been part of energy efficiency regulations and compliance calculations in Approved Document L since 2006. With every regulatory update since, in all parts of the UK, thermal bridging’s role has become increasingly important. Compliance is now much more challenging to achieve without taking proper account of thermal bridging. For projects looking to exceed building regulation requirements, low U-values plus minimal thermal bridging is a starting point for improvements in occupant comfort, surface condensation issues and building performance.
What is thermal bridging?
Thermal bridging is any break or reduction to the continuity of a building’s insulation layer (thermal envelope), and which results in greater heat loss locally compared to the surrounding building elements.
“Thermal bridging can account for as much as 30% of a building’s total heat loss,” says David Milner, Technical Team Lead at Celotex. “It was introduced to national building regulations because, as U-values for building elements improved, linear thermal bridging was an increasing proportion of overall heat loss.”
Where do thermal bridges occur?
This post focuses on linear thermal bridging. Throughout a building’s thermal envelope there are a host of junctions and details where the continuity of the insulation layer can be interrupted. Some of the most common include:
- The junction between the ground floor and external walls.
- The junctions between the external walls and a pitched or flat roof (eaves and gables).
- Around doors and windows (cills, lintels and jambs).
- Changes in the building geometry (external and internal corners of walls).
When little or no consideration is given to these areas of the construction, it is very easy for them to act as a weak point – a thermal bridge – in the building’s insulation layer. The result is a path for heat loss that circumvents what otherwise might be well-insulated building elements.
There are also point thermal bridges. These are isolated penetrations in the thermal envelope – for example, a rainscreen system bracket, or a steel beam – whose heat loss is expressed as a chi value. They are considered differently to linear thermal bridges and therefore don’t form a detailed part of our look at the role of linear thermal bridging in building regulation compliance.
How does thermal bridging relate to U-value calculations?
Another type of thermal bridging is repeating thermal bridges. Examples of these include fixings (like masonry cavity wall ties), or timber members (like stud frames or rafters).
Repeating thermal bridges still interrupt the insulation layer and can act as paths for increased heat loss. But they occur at regular intervals across the area of a building element (e.g., 400mm rafter spacing in a pitched roof).
There are mechanisms within the BS EN ISO 6946 U-value calculation method to account for repeating thermal bridges. As such, they do not need to be calculated separately, like linear thermal bridges. An online tool like Celotex’s U-value calculator gives the user the option to select accurate repeating thermal bridges.
What are the problems with thermal bridges?
Thermal bridges have the potential to be a key contributor to the performance gap between as-designed compliance and as-built performance. This is due to the relative complexity of designing them out initially. Then, once construction commences, it is often difficult to ensure proposed details are built in accordance with the design.
Approved Document L1 2021 says building fabric should be constructed “to a reasonable standard so that the insulation is reasonably continuous over the whole building envelope.”
When that “reasonable” continuity is not achieved, the building in use has higher rates of heat loss, energy use and carbon emissions than were predicted at design stage. It will also cost the building owner more in higher energy bills.
Another potential risk is surface or interstitial condensation due to “cold spots”, which can lead to mould growth; read more in our post about preventing condensation in buildings.
How do I know if I have thermal bridging: calculating linear bridging heat losses
Linear thermal bridges cannot be calculated using common U-value calculation methods. Instead, the detail must be thermally modelled in appropriate software. The result of the calculation is called a psi value.
Multiplying a psi value by the length of its corresponding junction gives the total heat loss for that junction. Repeating the process for all junctions in a building gives the total thermal bridging heat losses. Another way to express this is through a y-value, which is the thermal bridging heat loss as a percentage of a building’s total heat losses.
Needing to calculate so many different junctions and details can be an onerous prospect. For that reason, in the early 2000s, accredited construction details (ACDs) were published. They gave a standard approach (complete with installation checklist) to achieving reasonable psi values for common junctions.
However, ACDs were not updated and came to be superseded by a host of other detail libraries. No longer fit for purpose, and with industry now producing more relevant details, ACDs were removed when Part L 2021 was introduced in England.
“Alongside using standard details with pre-calculated psi values, it is also possible to obtain project-specific thermal bridging calculations,” explains David Milner. “Either approach tends to result in a lower psi value, which eases pressure on other areas of the building specification. For example, it may remove the need to over-specify insulation to achieve even lower U-values. Or it may reduce the amount of renewable technology needing to be deployed.”
How is Part L related to reducing thermal bridging?
For the purposes of carrying out compliance calculations, it has always been possible to use default values. This could be either default psi values for individual junctions, or a default y-value for overall thermal bridging heat losses.
With its view towards the Future Homes and Buildings Standards, Part L 2021 made the default values considerably worse, as previous default values did not accurately reflect real-world heat loss, so higher penalty values were introduced to incentivise project-specific psi-value calculations.
In addition, there are a range of measures designed to try and reduce the contribution that junction details make to the performance gap.
The insulation layer should be identified on drawings, and those drawings reviewed to ensure the layer is “continuous, buildable and robust.” Once on site, and before work is concealed, an audit should take place to assess that the designed details have been constructed. Photographs of key junctions form part of compliance reports.
How can I reduce thermal bridging by specifying insulation?
A good first step to reducing thermal bridging is giving more consideration to the placement of insulation in the main building elements.
Within a timber-framed wall, for example, rather than a between-and-inside frame insulation arrangement, a between-and-outside frame arrangement could be preferable. This is especially true if the pitched roof undergoes a similar change of approach and a warm roof structure is created, with the bulk of the insulation to the outside of the rafters.
Taken together, the external layers of insulation (such as Celotex GA4000) in the wall and roof can link almost seamlessly, creating continuity of insulation in a way that is also very buildable.
Of course, the timber-framed wall and the pitched roof could instead both feature internal layers of insulation that also join to create continuity. This is valid, as long as care is taken to avoid excessive and unnecessary penetration of the internal layers to run services. The advantage of using external insulation layers is that it moves the thermal envelope away from the services zone.
How do you fix thermal bridging in masonry cavity walls?
For a masonry cavity wall with the insulation layer in the middle of the wall, typical construction details feature a flexible insulation material at the eaves to provide the continuity between wall and roof.
“Whatever type of wall construction and insulation placement is chosen, the junction between ground floor and external walls can be difficult to detail,” David Milner acknowledges. “As the external walls transfer the building loads down to the foundations, there is almost always a break in the continuity of insulation to allow the wall structure to continue into the ground.”
Some of Part L 2021’s new guidance concerns this particular area. Perimeter upstand insulation (such as Celotex TB4000) between the floor slab and the face of the wall has long been a feature of floor details. Approved Document L1 2021 specifically states this should be a minimum of 25mm thick.
Thicker perimeter upstand insulation may be an option. For projects requiring particularly low psi values, a specialist load-bearing insulation product replacing a course of blockwork could also be an option. Details of junctions can be found in the Thermaclass Cavity Wall 21 Specification Guide.
How can Celotex expertise help with thermal bridging solutions?
Celotex delivers technical expertise and digital specification tools with system-wide solutions, including our popular online U-value calculator. We assist customers with project-specific advice aimed at minimising heat loss, as part of which we can direct them to external information sources like the recognised construction details for masonry wall build-ups.
The Celotex technical resource centre includes regulatory compliance documentation with performance certificates. Backed by this documented performance data, our support team provides verified calculations, construction details and regulatory guidance to help you create accurate specifications for standard and non-standard constructions alike.