Guide to polyisocyanurate (PIR) insulation
Polyisocyanurate, or PIR, is a type of thermal insulation which was developed as an advancement from polyurethane (PUR) insulation.
U-value Calculator
Start your U-value calculation
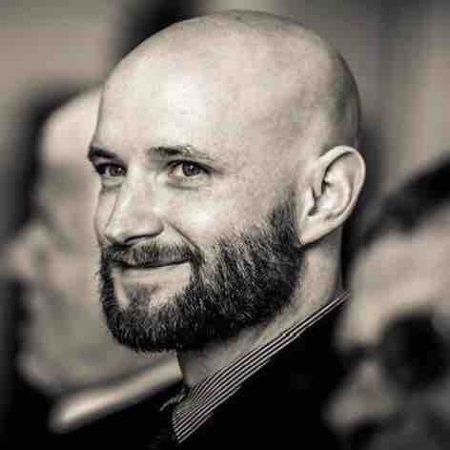
What is PIR insulation?
Polyisocyanurate, or PIR, is a type of thermal insulation which was developed as an advancement from polyurethane (PUR) insulation. Supplied as rigid boards that can be cut to size where needed, PIR insulation is used in a wide array of applications, from ground floors to flat or pitched roofs. It is used across a wide range of applications and sectors within floors, walls and roofs, though when used in external wall constructions is limited to a maximum height of 11m.
PIR insulation boards comprise a rigid foam core of relatively low density (around 30 kg/m3, and therefore often termed ‘lightweight’). They are faced on both sides, often with a composite aluminium foil facing. Other facings are used for specific applications, including glass tissue to receive flat roof membranes or kraft paper for bonding with plasterboard adhesive.
How does PIR insulation perform compared to other insulation types?
A key feature of PIR insulation is its relatively low thermal conductivity compared to many other insulation materials. With a typical lambda value for most applications in the region of 0.020-0.022 W/mK, comparatively thin layers of insulation are required to achieve the same thermal resistance as other insulation materials.
“All thermal insulation materials have a good thermal performance compared to other generic building materials. As such, insulation should be specified for the best combination of qualities to suit the goals of the individual project,” says David Milner, Technical Team Lead at Celotex. “Nevertheless, some insulating materials have lower thermal conductivities than others, and there are many design scenarios where thinner solutions are more advantageous or desirable – say, for reasons of space.”
Other types of insulation that PIR tends to be most readily compared with are other rigid foams like phenolic insulation (PF), extruded polystyrene (XPS) and expanded polystyrene (EPS). Depending on specific circumstances, PIR may be used in similar applications to wholly different insulation types like glass mineral wool and stone mineral wool (MW) or cellular glass (CG).
What are the advantages and disadvantages of PIR insulation?
The following table summarises some of PIR insulation’s key features, positives and negatives associated with those features, and contrasts with other insulation types where applicable.
Characteristic of PIR | Pros | Cons |
Widely available and versatile solution for a range of applications. | Popular product, especially with contractors and experienced DIYers. | Can lead to confusion between brands, products and application. |
Low thermal conductivity. | Can help to achieve lower U-values without significantly increasing thickness of construction. | Care required to avoid damaging foil facing and reducing performance; not an issue for unfaced insulation types. |
Large format board size (often 2400mm by 1200m). | Great for covering large areas, like ground floors, quickly and with minimal air gaps/board joints. | Can be unwieldy to handle, despite low density of foam. When cutting for more precise applications, care is required to achieve a tight fit. |
Compressive strength. | Suitable for bearing flooring loads associated with light usage such as domestic buildings. | Limited range of performance compared to insulation types such as XPS, EPS, and cellular glass. |
Moisture tolerance | Foam composition and aluminium foil facing provides good moisture vapour resistance, making it ideal for vapour closed constructions. | While moisture absorption is limited, PIR should not be left in contact with water, unlike XPS and cellular glass. Contact with water can damage the bond between the facing and foam, worsening thermal performance. |
Fire performance. |
As with any insulation material, it is important to distinguish between the reaction to fire performance of PIR on its own, and its ability to contribute to the fire resistance of a fully tested build-up alongside other components. Where necessary, advice should be sought from the manufacturer for project-and application-specific advice regarding fire behaviour. |
What is the life expectancy of rigid PIR insulation boards?
Product-specific technical information and third-party certification (e.g., BBA certificates) should always be checked to confirm statements about the durability and life expectancy of PIR insulation products.
When correctly specified, installed, and protected within the building envelope, PIR insulation can perform for the design life of the building. PIR insulation is not prone to rot and does not provide a nutrient source for vermin.
Correct specification and installation are key to getting the best from any PIR product. It is essential to seek a manufacturer’s advice about any use of PIR insulation, and the sooner the better. Once products have been installed and covered up, any remedial works will be expensive. Incorrect installation may result in compromised performance and costly remedial work.
Product literature and third-party certification should be the first port of call, supported by conversations with technical support teams.
Is the foil on PIR insulation a vapour barrier?
The foil facing on many PIR insulation products has a high resistance to moisture vapour, meaning it can provide a high level of vapour resistance and may function as part of a vapour control layer when correctly detailed.
First, the insulation layer must be continuous so the whole area of the building element is covered by the foil facing (insulation boards interrupted by timber rafters, for example, would be ineffective). Then, the boards must be tightly butted to avoid air gaps between them. Finally, every board joint must be taped with a suitable product capable of resisting air and moisture movement.
If warm, moist air can pass through the insulation layer and into the structure, then there is a risk of interstitial condensation alongside increased rates of heat loss.
What applications can PIR insulation be used in?
The ability to manufacture PIR insulation in a variety of board sizes, with different facings, means it is possible to create solutions for a range of applications.
- Ground floors
In solid concrete floors, PIR boards can be installed above or below the floor slab. Designs should ensure the insulation boards are protected from ground water below by a damp proof membrane (DPM), and from concrete slabs or screeds above by an air and vapour control layer (AVCL).
Similarly, boards can be laid on a suspended block and beam deck, again with an AVCL cover. The need for any DPM depends on site conditions.
The insulation can be cut to fit between suspended timber floor joists. “This is less common in new-build projects,” says David Milner, “but retrofit projects may well feature suspended timber ground floors. Advice should be sought about ensuring sufficient ventilation in the floor void and protecting joist ends from moisture damage as part of energy efficiency upgrades.”
- External walls
By far the most common use of PIR insulation boards in external walls is for masonry cavity wall applications. Supplied in a smaller format board size of 1200mm x 450mm, the insulation fits typical wall ties spacings. It may also feature a tongue and groove edge profile to help achieve a better fit.
Traditionally, PIR insulation was supplied for masonry cavity walls as a partial fill solution, with a 50mm (and sometimes 25mm) air gap between the outer leaf masonry and the insulation. In the last decade, so-called ‘full fill’ cavity insulation solutions have appeared on the market, reducing the air gap to around 0-10mm and allowing greater performance to be achieved without increasing cavity widths.
For any masonry cavity wall application, the chosen insulation should have current third-party certification, like a BBA certificate. Our guide to masonry cavity walls goes into this application in more detail.
Timber framed walls can feature PIR boards, with the insulation installed as a continuous layer on either side of the frame, and insulation cut to fit between the timber studs too. Precise arrangements depend on the specifics of the wall build-up, such as the choice of external finish, the proposed airtightness and vapour control strategy, and whether service voids are to be incorporated. See also the section on modern methods of construction (MMC) below.
For internal wall insulation (IWI) applications, plasterboard-bonded PIR solutions have been used in the past. However, better understanding of the moisture behaviour of traditional solid walls has led to this type of installation becoming less common. The vapour-closed nature of PIR insulation is often unsuited to vapour open solid walls. The Celotex technical team can provide further advice in this regard to help you make informed decisions.
PIR insulation is less commonly used for external wall insulation (EWI) systems, as alternative insulants are often more widely used in EWI due to render compatibility and cost considerations.
- Pitched roofs
PIR insulation can be used above, above and between, or between and under pitched roof rafters. Where a layer of insulation is installed above or below the rafters, the large format size of PIR boards is advantageous for covering bigger areas with fewer board joints.
Where designed as part of the vapour control strategy, below-rafter PIR insulation may be taped along board joints to contribute to the air and vapour control layer (AVCL) function.
For between-rafter insulation layers, insulation boards obviously need to be cut to fit. Cutting should be planned as carefully as possible to reduce the volume of waste offcuts.
“The relatively thin layers of PIR insulation required to meet national building regulation requirements makes it a common choice for loft/room-in-a roof conversion projects,” explains David Milner. “Pitched roof insulation is installed as normal. Boards can either continue down the slope of the roof to the eaves or be used to insulate half-height timber stud walls.”
Where a cold roof space is being retained and ceiling-level insulation being upgraded or replaced, it is possible to install PIR boards between and over the joists. It can be possible to create a walkable surface in this way, but there are main considerations:
1. large format boards for loft insulation will need to be cut and then carried up through the loft hatch into the roof space; and
2. the interaction of the new insulation with any existing insulation and eaves ventilation, alongside whether the top floor ceiling is well-sealed or not, to avoid potential condensation issues.
3. The suitability of any access decking, including its fixing method and load-bearing capacity, which should be designed and assessed to ensure safe support for intended access or storage loads.
- Flat roofs
Insulation boards offered for warm flat roof applications can feature facings other than aluminium foil. Foil faced boards are still offered where single ply membrane waterproofing is mechanically fixed. For specific types of flat roof waterproofing, glass tissue or bitumen-based facings provide compatibility for direct bonding of the waterproofing directly to the insulation board.
Regulatory requirements to do with fire spread across flat roofs, and fire penetration through roof structures, means there is an established testing regime for flat roof systems. PIR insulation is frequently part of such testing and contributes to the systems achieving suitable performance for most situations and boundary conditions.
- Panel systems and modern methods of construction (MMC)
For specifiers looking to take advantage of the speed and quality benefits of offsite manufacture, it’s worth noting that many manufacturers of panellised systems use PIR insulation as part of their designs. Timber and steel framed solutions are precisely designed to utilise PIR insulation’s thermal performance characteristics. Such products are routinely used in housebuilding. For non-domestic buildings, PIR insulation can be used within wall and roof panel as part of systems designed to achieve the overall buildings performance requirements.
How is PIR insulation made?
The production line for PIR insulation starts with the liquid foam mixture being set down on the back of the facing material. A substance called a blowing agent instigates a chemical reaction that causes the liquid to expand rapidly, and it rises to meet the underside of the other facing. The distance between the two facings is controlled to give the desired board thickness.
On the constantly moving production line, this initial phase happens in a matter of seconds. The material passes into an oven to be ‘cooked’ and then undergoes an extended cooling process designed to stabilise and flatten the boards. The latter stages of the production process see the boards trimmed, cut, packaged and, finally, moved to the warehouse to cure.
The chemical reaction creates the foam structure which, together with the trapped gases, delivers the thermal insulation properties associated with PIR insulation. As David Milner describes: “It creates a foam with a closed cell structure. The gas trapped in the cells of the foam which has a lower thermal conductivity than air, contributing to the insulation's thermal performance. Over time, some diffusion of the gases occurs, which is accounted for in the declared long-term thermal performance.”
What is the thermal performance of PIR insulation?
Like any insulation material, a PIR board’s thermal performance is expressed in two different ways.
- The thermal conductivity, or lambda value, is a property of the material itself, independent of thickness. If a product’s declared lambda is 0.022 W/mK then that is the case for a board 25mm thick or 150mm thick.
- To differentiate between different product thicknesses, a thermal resistance (R-value) is also declared. An R-value is calculated by dividing the thickness by the declared lambda. For a 25mm board of 0.022 W/mK lambda, the R-value is 0.025 / 0.022 = 1.136 m2K/W. A 150mm board has an R-value of 0.150 / 0.022 = 6.818 m2K/W.
Lambda values help to show the relative performance levels of different materials. R-values are needed to establish what thicknesses of different products offer equivalent performance, when comparing purely in terms of thermal efficiency.
R-values of all building materials, including thermal insulation, are used in U-value calculations to establish the overall thermal transmittance of a complete building element. Required product thicknesses are very much project specific, depending entirely on the target U-values that need to be achieved to meet the project’s overall goals (see the following section on sustainability).
Do PIR insulation boards need an air gap?
An added benefit of the foil facing of most PIR insulation boards is that it can help to achieve additional thermal performance from a build-up. When the aluminium foil is ‘low emissivity’ and faces into an air space, it changes the nature of heat transfer across that air space. When carrying out the U-value calculation, the thermal resistance of the air space can be increased.
There is a further increase if an air space is bounded on both sides by low emissivity surfaces – whether that is a PIR board or a reflective membrane. The precise extent of the low emissivity benefit depends on the depth of the air pace, and whether the construction is a floor, wall or roof (as this affects the direction of the heat flow).
Some applications require an air gap for specific performance reasons. For example, when using a partial fill PIR board in a masonry cavity wall, the clear cavity between the insulation and the outer leaf brickwork is critical to preventing moisture ingress through the wall build-up. The insulation board is able to take advantage of the required air gap, with the low emissivity facing contributing some additional thermal performance.
Is PIR insulation sustainable?
The harmonised European standard that sets out the technical specification for PIR insulation products, BS EN 13165, includes the following statement: “The reductions in energy used and emissions produced during the installed life of the insulation products exceeds by far the energy used and emissions made during the production and disposal processes.”
This statement highlights the long-term energy and emissions benefits associated with the use of insulation products, including PIR. Without thermal insulation products, it would be impossible to achieve the kinds of U-values necessary to reduce energy use, limit carbon emissions from the built environment and prevent new buildings from being cost prohibitive to run.
National building regulations set the minimum standards for energy efficiency. Other voluntary standards exist which a project can meet to achieve better than the minimum. Arguably the best known of these is the Passivhaus standard. PIR insulation can be incorporated into designs seeking Passivhaus certification, provided all relevant design and detailing requirements are met. In such situations, there will be an even greater benefit to the occupants in terms of long-term savings on energy demand.
Sustainability, however, is a complex topic. At its broadest, sustainability is a diverse array of complex and interconnected issues. One project’s definition of being sustainable could be very different to another’s. As such, sustainability goals should be specific to individual projects – whether that is meeting a particular standard (or set of standards) or aligning with the client’s values.
There can be no disguising, therefore, that PIR is a material derived from petroleum and its manufacture contributes to ongoing fossil fuel extraction, with all of the attendant impacts. However, it can also be said that, as a low-density material whose cellular structure is mostly gas, it’s possible to derive a large volume of the material for the carbon emissions incurred.
“Carbon emissions are one of the primary measures by which the construction industry judges the sustainability of its activities,” says David Milner. “The low operational emissions made possible by the use of insulation products like PIR are a considerable success story. The focus is now moving onto embodied and whole life carbon, or the emissions incurred either side of a building’s operational phase.”
We have just touched on the raw material sourcing and manufacturing phases; we must also consider the end-of-life phase when a building is no longer useful. What happens to the insulation material that comes out of a building during deconstruction and demolition?
The chemical nature of PIR foam, combined with the facing materials adhered to it, mean any insulation boards recovered from buildings cannot be recycled to make new insulation boards. If they cannot be reused on another project – and they would have to be in perfect condition to do so – then the only option is to dispose of them in some way.
The wording quoted above suggests the carbon emissions associated with this are an acceptable trade-off given the carbon reductions evidenced during the building’s useful life. Nevertheless, burning waste insulation for energy or sending it to landfill are the lowest two options on the hierarchy of waste. As the whole construction industry looks to achieve greater circularity in its material choices, it is necessary for the wider insulation sector to be open about its products still being very much part of the linear economy.
Thanks to global efforts to reduce the use of global warming-causing substances, one element of insulation manufacture that has improved from a sustainability perspective is the blowing agents. Where previously HFCs and HCFCs with very high global warming potential (GWP) were commonly used in PIR manufacture, they have been replaced by alternatives with low GWP and zero ozone depletion potential (ODP).
How should PIR insulation be installed?
For any insulation type, PIR included, to deliver the intended thermal performance of a building, it must be installed correctly. That means ensuring it is in a continuous layer, with as few air gaps as possible. It should also be continuous from one element to another (i.e., at floor/wall junctions or wall/roof junctions); this is explicitly stated in current technical guidance supporting national building regulations.
PIR insulation products for ‘general’ applications – floors, framed walls, pitched roofs – are typically supplied in large board sizes. They are especially well suited to situations in which they don’t need to be cut to fit between joists or rafters, as they can cover large areas and minimise the risk of air gaps occurring.
‘Easy to install’ is a subjective term that is difficult to qualify precisely. For experienced contractors used to working with insulation products, taking advantage of the large board size should be relatively straightforward.
“For any installer, experienced or otherwise, the need to cut boards to size to fit framing systems or between joists/rafters presents more of a challenge,” David Milner acknowledges. “A tight fit must be achieved, between the insulation and the surrounding framing/joists/rafters, and between different pieces of insulation. Otherwise, air gaps allow warm air to bypass the insulation and reach the cold side of the insulation.”
That warm air can also carry moisture vapour which, if it comes into contact with colder surfaces, could present a condensation risk. Any such failings in the construction of building fabric contribute to the problem of the performance gap, where energy use and carbon emissions are worse than predicted by compliance calculations.
Masonry cavity wall applications are particularly sensitive to installation issues. Excess mortar on the face of the inner leaf masonry causes the surface of the blockwork to become uneven; installing rigid insulation boards needs a flat surface for the insulation layer to be most effective. By their nature, the boards can’t flex or mould themselves to any undulations, and any damage to the foil facing risks worsening the thermal conductivity of the board. A high standard of workmanship is required in all applications, but particularly in masonry cavity walls to minimise the risks of thermal bypass.
A final point to note on installation is that PIR insulation boards should never be used in a situation where prolonged exposure to water is possible. While the foam has a relatively low rate of moisture absorption (albeit not the lowest of rigid foam insulation types), water will still impact on thermal conductivity and potentially contribute to the facing material coming away from the foam.
How much does PIR insulation cost?
Offering a precise cost of PIR insulation is difficult. Material prices across the construction industry have been subject to significant rises since the Covid pandemic and continue to be volatile.
Allied to that is the range of stockists who offer PIR boards, from well-known national merchants with large branch networks to online outlets. Costs vary depending on supplier, and on an individual contractor’s terms with their preferred stockist.
What can be said generally is that insulation costs tend to increase as thermal conductivities lower.
Being at the more thermally efficient end of the insulation spectrum, PIR generally carries higher material costs compared to some alternative insulation types – in addition to factoring in the costs associated with its raw materials and the technology required in the manufacturing process. Understandably, thicker boards are more expensive than thinner boards.
As touched on earlier, however, insulation contributes to reduced energy demand, which can support lower energy consumption over the building’s life. David Milner says: “The better the standard of energy efficiency achieved overall, the lower the energy demand. As such, specifying insulation to meet the intended thermal performance is an important aspect of long-term energy management and should be carefully considered early in the process.”
There is a reason that ‘more sustainable’ construction is usually cited as being more expensive. But efficient and sufficient designs help to keep costs under control by avoiding over-specification and over-consumption. Labour costs can be controlled through using experienced and diligent contractors, perhaps with some investment in training for them. Or offsite manufacturing can be used to help reduce the amount of on-site labour required.
For example, one Scottish housebuilder has found that adopting their own manufacturing has allowed them to build A-rated homes for around 10% less1 than a typical C-rated home might cost another housebuilder to construct.
Conclusion: how can PIR insulation benefit my project?
Thanks to its versatility and the number of applications in which it can be used, there is a broad selection of PIR insulation boards to choose from. Not only in terms of the number of PIR manufacturers, but the number of different boards within each manufacturer’s range.
In the broadest terms, there is little to differentiate between the core foam in each product. Products offered for different applications often have the same thermal conductivity and often appear to have the same foil facing as well. It’s little surprise that it can prove confusing for specifiers and, in particular, installers who have to purchase from what stockists have available.
There are differences, however. Visibly, different board sizes are produced to suit specific applications – masonry cavity walls especially. From a paperwork perspective, declarations of performance (DoPs) and independent certification (including BBA certificates) are product specific. Responsible design and specification decisions rest on using the right product in the right application, with the correct supporting evidence where projects require it.
When this is backed up by a standard of installation that helps the insulation to deliver on its performance characteristics, then PIR boards offer the following benefits.
- Low thermal conductivity that helps to achieve low U-values without substantially increasing the thickness of constructions.
- Contribute to meeting requirements of national building regulations and, where required, other voluntary standards.
- As part of a considered design and specification, PIR insulation can contribute to reducing operational energy demand and supporting occupant comfort.
- Widely available material capable of being used in a range of applications, with a host of thickness options.
- High level of technical support from well-known manufacturers, including the availability of tools such as online U-value calculators with condensation risk analysis functions.
For project-specific technical advice on specifying Celotex PIR insulation, please contact our technical services team.
Free online tools from Celotex
The Celotex online U-value calculator has long been a valuable tool. Its functionality has now been enhanced to include condensation risk analysis (conducted using the Glaser method) alongside combined-method heat loss calculations.
Users can obtain U-value calculations and, for construction types recommended by BS 5250:2021, condensation risk analyses at their convenience. Technical specifications and installation guidance for Celotex products are also available, allowing for project-specific specification development.
Discover more about our comprehensive calculation tools, including U-value and condensation risk analyses. For construction types not covered by the combined method or Glaser method, contact our technical support centre for expert advice.