How Celotex’s Technical Team adds value through expert insulation support
Creating buildings designed for reliable thermal efficiency isn’t simply about material selection. It demands precise understanding of how insulation integrates with the entire building fabric.
U-value Calculator
Start your U-value calculation
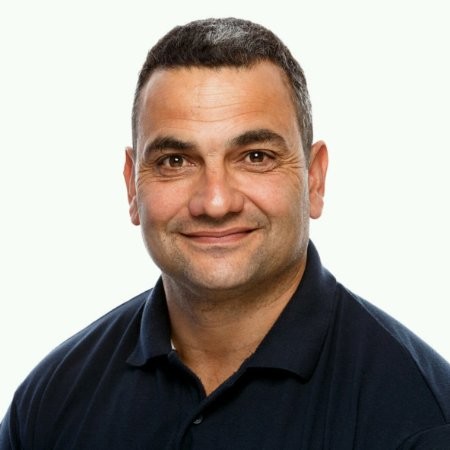
Creating buildings designed for reliable thermal efficiency isn’t simply about material selection. It demands precise understanding of how insulation integrates with the entire building fabric. That’s where Celotex's Technical Team comes in, drawing on their decades of combined experience to offer reliable technical insulation support for different stages of the construction process.
The acquisition of Celotex by SOPREMA has further strengthened this technical insulation expertise, integrating the knowledge and resources of both teams.
So, who are the technical specialists making sure installers and customers get the best from Celotex products? We spoke to Mike Vaczi, Technical Director at SOPREMA, and Team Leader, David Milner, to find out.
Meet the team driving insulation expertise and innovation at Celotex
Mike’s experience is built from the ground up. Starting out as a site hand in the roofing and waterproofing industry, he worked his way through an apprenticeship before leading teams across the South of England. This deep practical knowledge, combined with his expertise in working with major insulation brands, made his transition into technical leadership a natural step.
“I worked my way up from being a site hand to running teams and training apprentices,” he says. “For years, I was on-site every day, making sure installations were done to a high standard, whether in schools, colleges or local authority buildings. That hands-on experience now means I understand exactly what installers need to get the job done right.” These early years even included working with SOPREMA and Celotex products, until he eventually joined SOPREMA as a site technician over a decade ago.
Now Technical Director, Mike navigates everything from site training to technical management, overseeing rigorous product testing and certification. He’s a key figure in Celotex’s Technical Team, ensuring every product meets strict regulatory standards and performs reliably in real-world applications.
When you're guiding specifiers through complex insulation decisions, you need someone who understands precision. His Team Leader, David, provides just that. With a background in geophysics and petroleum engineering, David is no stranger to this level of accuracy. But what brings someone from studying seismic waves to specifying insulation?
“My background is really mixed,” David explains. “My undergraduate was geophysics then I went on to do a Masters in Petroleum Engineering. Then the economic crash happened, so I tried a bit of everything, including air traffic control for a while! Though I must say, helping builders get their insulation right is slightly less stressful than landing planes.”
So what was it about the construction industry that appealed to David? “It’s about helping create better buildings,” he says. “Whether that’s through our PIR boards in a timber frame wall or our XPS products in a basement application, every project is an opportunity to improve building performance.”
And what about Mike? For him, the appeal lies in ensuring insulation performs not just in theory but in real-world applications. “You can talk about a product all day,” he says, “but in the real world, it’s about how installers perceive it, how they use it, and whether it performs as expected.”
A day in the life: How Celotex’s Technical Team solves real insulation challenges
“There’s really no such thing as typical,” David says. “One morning, we could be reviewing BBA documentation for our PIR boards, by lunch we might be helping a house builder solve a tricky cavity tray detail. Then in the afternoon, I could be training our sales team on the key differences between PIR versus XPS in below-ground applications.”
Sometimes, technical support means the team getting their boots dirty. For example, when housebuilders were asking for a solution to avoid moisture ingress at stepped cavity trays without sacrificing thermal performance, we reached out to Visqueen, a provider of construction membrane technologies, to collaborate with their technical team at their training centre to develop a solution. We then rolled this out to site to see if it performed as expected in a real world environment.
“While we don't routinely visit sites, some problems need a hands-on approach,” David explains. “Our sales team identifies installation challenges, then we work out solutions. With the stepped cavity tray detail, we ended up creating new CAD drawings and updating our specification guide for thermaclass. That way, when one builder faces an issue, everyone benefits from the solution.”
While David and the team are handling day-to-day Celotex insulation support, a team Mike refers to as “very well qualified and capable,” Mike himself is overseeing the bigger picture, with much of his time dedicated to BBA certification. His responsibilities span multiple brands and manufacturing sites, where he ensures that everything from initial product testing to on-site installation guidance meets the highest standards. He says: “It starts with how the product is made, tested and verified to be fit for purpose before it even reaches the market.”
And then there’s the fact that U-values need to be worked out correctly, ensuring everything the Celotex team communicates aligns with Part L and Building Regulations. “We have a role to play helping installers get it right on-site too, following our recommendations as the manufacturer. For us at Celotex and SOPREMA, it’s very, very important that the correct information we put out is must be unambiguous. We’re not just giving them a product. We’re making sure they understand how it fits into the whole system. That means advising on everything from correct installation to condensation risk, so moisture issues are avoided down the line."
The team prides itself on its commitment to rapid response, too: most queries receive initial feedback within an hour, with full resolution typically within 24 hours. “Whether you're a self-builder, an installer, a contractor or a major housebuilder,” David says, “you'll get exactly the same level of service. Every query gets looked at, every question gets answered. It's about what you need, not who you are.”
Best practice in retrofit insulation: How technical guidance prevents condensation issues
Technical expertise is crucial when it comes to retrofit projects. The UK’s existing building stock presents unique challenges, particularly when it comes to improving thermal performance without creating condensation issues.
“This is where our range of both PIR and XPS products really comes into its own,” David explains. “Different situations demand different solutions. Sometimes you need the high thermal performance of PIR boards, other times the moisture resistance of XPS might be important. Particularly in below-ground applications.”
To help with this, the team is developing guidance through the Celotex Guide to Retrofit, which will help specifiers understand exactly where and how to use different insulation types effectively. As Mike explains: “The information we put out must be unambiguous and align with Building Regulations. From how a product is installed on-site, to ensuring it meets compliance, every detail matters.”
Looking ahead: Where does the team see the future of insulation heading?
If you ask Mike and David, the changes ahead will transform how we think about insulation.
“We're seeing a fundamental shift in how buildings are constructed,” David notes. “Modern Methods of Construction (MMC) are gaining momentum, particularly in timber frame house building. This brings fresh challenges around airtightness and thermal bridging. It's not enough to just look at U-values anymore.”
Looking further ahead, David sees the UK construction industry moving away from traditional cavity walls. “We're heading towards thinner, more airtight structures with mechanical ventilation systems,” he explains. “That's why we need to think about buildings as complete systems. A wall specification isn't just about the wall anymore. It's about how that wall works with every other element. Does it support the ventilation strategy? How does it impact airtightness? How can we reduce thermal bridging? These are the questions we need to answer now.”
Sustainability is another key driver shaping the future of insulation, according to Mike. “The carbon footprint of insulation is going to be at the forefront in years to come,” he says. “It’s not just about how an insulation product performs during its lifetime, but also how it’s made. Exploring alternative raw materials is a key focus moving forward."
As part of all this, the team is focused on contributing to advancements in building science through their professional development. David is currently pursuing Passive House consultancy certification, reflecting the industry’s evolution towards more sophisticated approaches to thermal performance. The team is also working with the Insulation Manufacturers Association (IMA) to standardise U-value calculations across manufacturers, helping to align technical standards across the industry.
They’re continually enhancing their processes to ensure transparency and accuracy in product performance claims. “For us at Celotex and SOPREMA, it’s absolutely vital that the information we put out is unambiguous and correct,” says Mike. “It has to be right from the start. How the product is made, how it’s tested, and how it’s installed on-site. All elements must be meticulously accounted for.”
And that's why the Celotex Technical Team is so adept at helping construction professionals navigate insulation challenges with clear, reliable technical guidance.